Precision and efficiency are critical in plasma cutting, whether for industrial fabrication, automotive repair, or DIY metalworking. One of the most crucial aspects of achieving clean, accurate cuts is proper torch height control, which ensures the plasma torch maintains the optimal distance from the workpiece. Without it, cut quality deteriorates, leading to excessive dross, uneven edges, or even torch damage.
This article explores four essential topics for optimizing your plasma cutting system:
Torch Height Control – The foundation of precise plasma cutting.
Plasma Cutter Setup – Configuring your machine for optimal performance.
THC Screen Set Mach3 – Integrating torch height control with CNC software.
Torch Height Control Test – Verifying system accuracy before cutting.
By understanding these components, you can maximize cutting quality, extend consumable life, and minimize errors.
Torch Height Control – The Key to Precision Cutting
Torch height control (THC) is one of the most critical factors in achieving high-quality plasma cuts. Whether you’re working with thin sheet metal or thick steel plates, maintaining the correct distance between the torch and the workpiece ensures clean edges, reduces consumable wear, and improves overall efficiency. Without proper torch height control, even the most advanced plasma cutter can produce inconsistent results, leading to costly rework and material waste.
Why Torch Height Control Matters
The primary function of torch height control is to keep the plasma arc at an optimal standoff distance from the material being cut. This distance affects:
- Cut Quality – Too close, and the torch may drag, causing nozzle damage. Too far, and the arc weakens, resulting in excessive dross and uneven edges.
- Consumable Life – Proper torch height control prevents premature wear of electrodes and nozzles by avoiding contact with molten metal.
- Arc Stability – A consistent standoff distance ensures a stable plasma arc, which is crucial for smooth, precise cuts.
Most modern torch height control systems use either mechanical sensors, capacitive sensing, or voltage-based feedback to adjust the torch position in real time.
How Torch Height Control Works
There are two main types of torch height control systems:
Initial Height Sensing (IHS) – Before cutting begins, the torch lightly touches the material or uses a sensor to detect the surface and set a starting height.
Voltage-Based THC – During cutting, the system monitors arc voltage and adjusts the torch height dynamically to maintain a consistent arc length.
For example, if the material warps due to heat, voltage-based torch height control will raise or lower the torch to compensate, ensuring continuous precision.
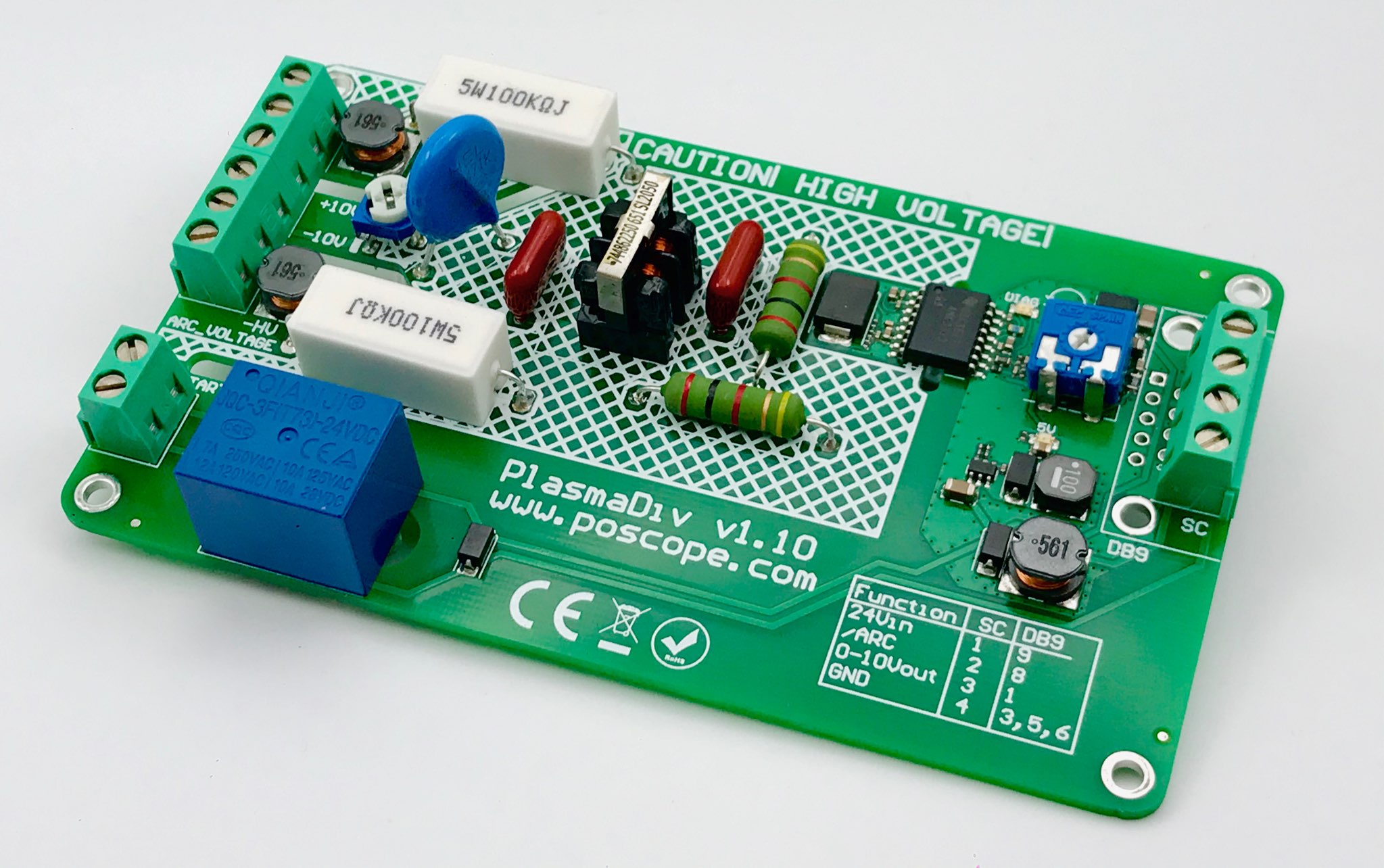
Common Challenges and Solutions
Even with an automated THC system, issues can arise:
- Uneven or Warped Material – A good THC system should compensate for surface variations.
- Electrical Interference – Proper grounding and shielded cables help maintain accurate voltage readings.
- Incorrect Settings – Calibrating the THC for different materials and thicknesses is essential.
By fine-tuning torch height control, operators can significantly improve cut quality and machine longevity.
Plasma Cutter Setup – Optimizing Your Cutting Performance
Proper plasma cutter setup is essential for achieving clean, efficient cuts while working in harmony with your torch height control system. Whether you’re a hobbyist or a professional fabricator, understanding how to configure your machine correctly can mean the difference between flawless results and frustrating failures.
Key Components of Plasma Cutter Setup
Before making your first cut, several critical elements of plasma cutter setup must be checked:
Power Supply & Amperage Settings
Match the amperage to the material thickness. Too high can cause excessive kerf width, while too low may result in incomplete cuts.
Ensure stable power input to prevent voltage fluctuations that could interfere with torch height control.
Air Pressure & Gas Quality
Clean, dry air is crucial for plasma arc stability. Moisture or oil in the lines can lead to poor cut quality and premature consumable wear.
Most systems require 90-120 PSI, but always consult your machine’s manual.
Torch Consumables
Inspect the nozzle, electrode, and shield cup for wear or damage before each use.
Using worn consumables increases the risk of erratic arc behavior and poor cut edges.
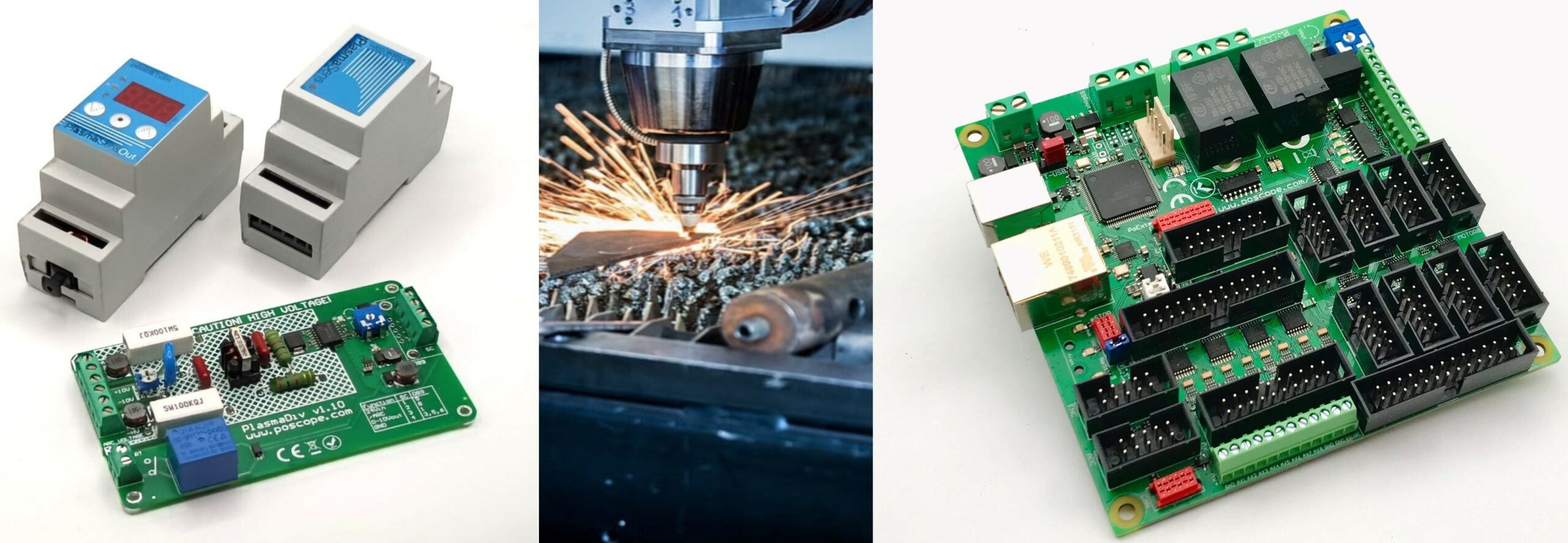
Grounding & Work Clamping
A solid electrical connection between the workpiece and the ground clamp ensures consistent arc performance.
Poor grounding can cause arc flickering and interfere with torch height control.
Integrating Plasma Cutter Setup with Torch Height Control
For automated systems, your plasma cutter setup must be synchronized with the THC for optimal performance:
- Pierce Height vs. Cut Height –
- The torch should pierce at a higher position (typically 1.5–2x the cut height) to avoid splatter damaging the nozzle.
- After piercing, the THC should lower the torch to the optimal cutting distance.
- Feed Rate & Voltage Matching –
- Cutting speed affects arc voltage; if the machine moves too fast or slow, the THC may struggle to maintain proper height.
- Adjust feed rates based on material thickness and amperage settings.
Troubleshooting Common Plasma Cutter Setup Issues
Even with careful preparation, problems can occur:
- Excessive Dross or Slag – Usually caused by incorrect speed, amperage, or torch height.
- Uneven Arc or “Wandering” Cuts – Often due to poor grounding, worn consumables, or electrical interference.
- Torch Collisions with Material – Indicates a malfunctioning THC or incorrect initial height sensing.
By mastering plasma cutter setup, you ensure that both manual and CNC-assisted cuts are precise and repeatable.
THC Screen Set Mach3 – Configuring Your CNC Control System
For CNC plasma cutting operations, properly setting up the THC screen set Mach3 interface is crucial for seamless integration between your torch height control and cutting software. Mach3, one of the most widely used CNC control programs, offers specialized THC screens that allow precise monitoring and adjustment of your height control system during operation.
Understanding the Mach3 THC Interface
The THC screen set Mach3 provides operators with real-time control over critical height adjustment parameters:
- Voltage Monitoring Display – Shows actual arc voltage versus your target voltage
- THC Enable/Disable Toggle – Allows manual override when needed
- Height Adjustment Controls – Fine-tune the Z-axis position during cuts
- Fault Detection Indicators – Alerts for loss of arc or height control issues
Proper configuration of the THC screen set Mach3 ensures your automated height control responds correctly to material variations and maintains optimal cut quality throughout the job.
Step-by-Step THC Screen Configuration
Load the Plasma THC Profile
Select the dedicated plasma cutting profile in Mach3
Verify all motor tuning settings match your machine specifications
Set Voltage References
Input your target arc voltage based on material thickness
Configure acceptable voltage deviation thresholds
Adjust Response Parameters
Set THC reaction speed (too fast causes oscillation)
Configure delay times for pierce sequences
Enable Safety Features
Activate anti-collision settings
Set soft limits for Z-axis travel
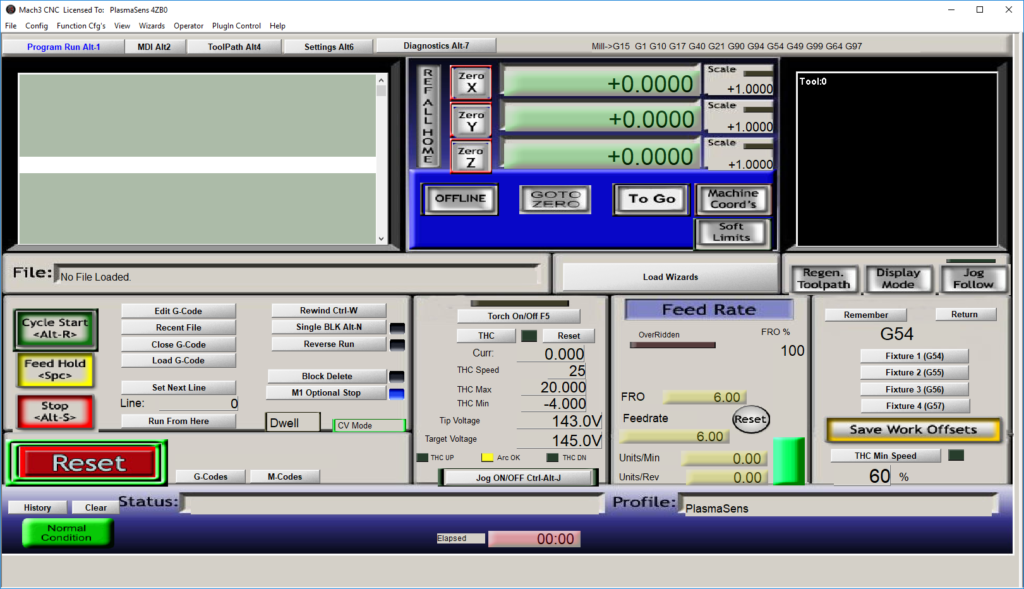
Troubleshooting Mach3 THC Operation
Common issues with THC screen set Mach3 include:
- THC Not Engaging – Check enable signals and voltage calibration
- Erratic Height Adjustments – Adjust PID settings in configuration
- Screen Freezes – Verify computer meets Mach3 system requirements
The THC screen set Mach3 provides diagnostic tools to help identify and resolve these problems quickly, minimizing downtime.
Advanced THC Screen Features
Experienced operators can utilize:
- Custom macros for complex cutting sequences
- Data logging to analyze performance over time
- Multi-cut profiles for different material types
Mastering the THC screen set Mach3 gives you complete control over your plasma cutting process, ensuring consistent results across all your projects.
Torch Height Control Test – Ensuring Cutting Precision
Performing a comprehensive torch height control test represents the final safeguard before committing to production cuts. This critical verification process examines whether all system components—from mechanical sensors to CNC software integration—function together to maintain precise torch positioning throughout the cutting operation. Neglecting this step risks costly errors that could otherwise be prevented through systematic validation.
The Critical Importance of Testing
The consequences of skipping a torch height control test manifest in several damaging ways. Nozzle crashes become likely when height sensing fails, resulting in immediate consumable damage and unexpected downtime. Inconsistent cut quality emerges when the system cannot maintain proper arc length, creating uneven edges that require additional finishing work. More seriously, undetected faults in the height control system may only reveal themselves during complex cuts, leading to scrapped workpieces and schedule delays.
A properly executed torch height control test examines multiple performance aspects simultaneously. Initial height sensing accuracy determines whether the torch approaches the material at the correct pierce distance. Dynamic adjustment capability proves whether the system can compensate for material warping during cutting. Voltage monitoring reliability confirms the feedback loop maintaining arc consistency, while collision avoidance functionality protects against catastrophic torch damage. Together, these tests provide operators with complete confidence in their system’s readiness.
Executing the Testing Process
Manual height verification forms the foundation of any torch height control test. Using precision feeler gauges, operators confirm the torch stops at the programmed pierce height with consistent repeatability. The retract distance after piercing requires equal scrutiny, ensuring the torch lifts to the proper cutting height without excessive delay. Testing on angled surfaces reveals whether the system maintains consistent standoff distance when encountering uneven material, a common challenge in real-world cutting scenarios.
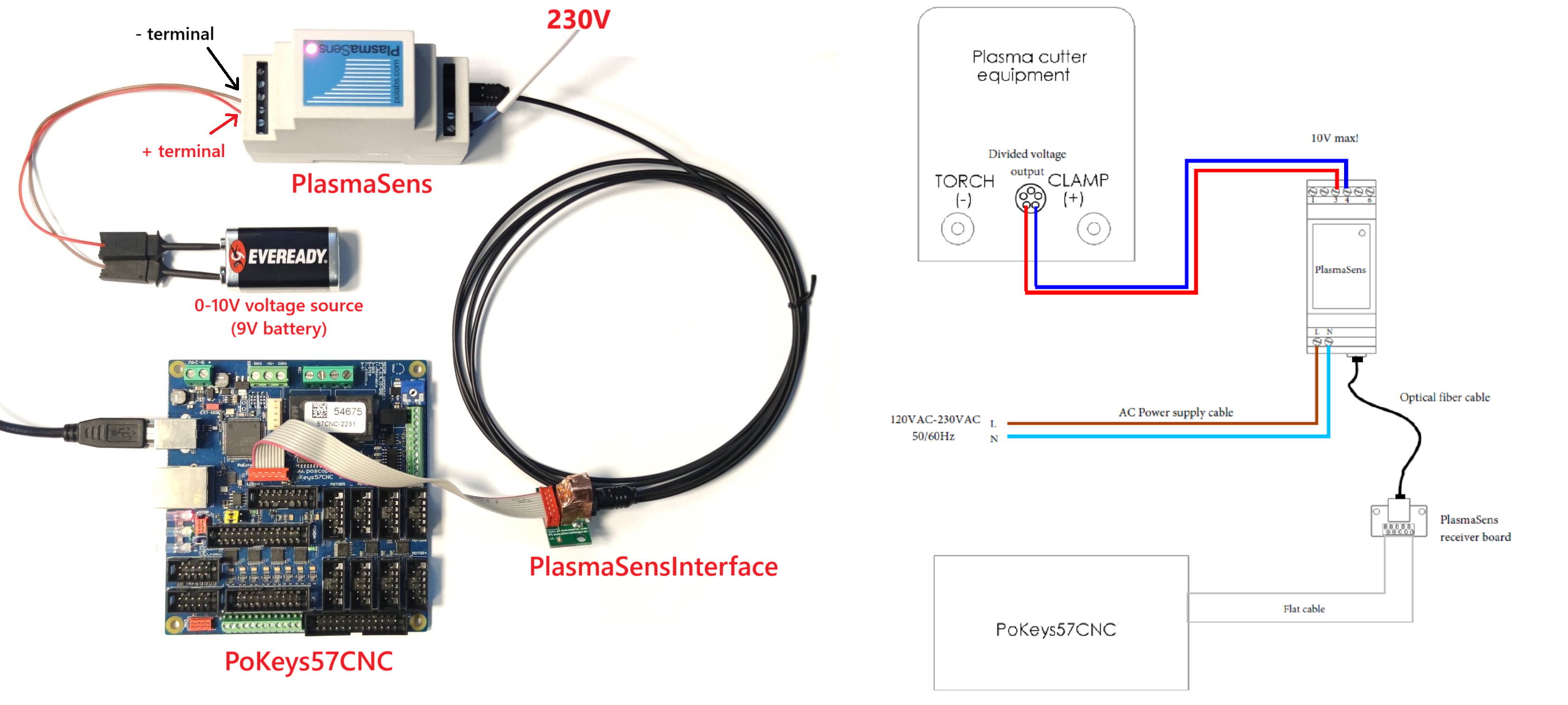
Dynamic response testing pushes the system beyond basic functionality checks. Cutting across intentionally warped material demonstrates the THC’s ability to compensate for surface variations while maintaining cut quality. Observing the Mach3 THC screen during these tests provides visual confirmation of proper voltage tracking and adjustment behavior. The Z-axis movements should appear smooth and controlled, without the telltale oscillation that indicates poorly tuned response parameters. These dynamic tests prove the system can handle the unpredictable conditions encountered in actual production environments.
Failure scenario testing completes the comprehensive evaluation. Simulating lost arc conditions verifies whether safety protocols engage appropriately to protect both equipment and workpiece. Material proximity sensors require testing across different metal types to confirm consistent performance regardless of material characteristics. Emergency stop functionality demands particular attention during THC operation, as this represents the last line of defense against catastrophic collisions. Only after successfully navigating these simulated failure conditions can operators trust their system’s reliability.
Analyzing and Documenting Results
A successful torch height control test produces several definitive indicators of proper system function. The arc voltage should remain stable throughout cutting operations, varying no more than ±2V from the target value. Height transitions should occur smoothly, without abrupt or jerky movements that suggest mechanical or control issues. Perhaps most telling, the nozzle should emerge from piercing tests without signs of splatter buildup or damage, confirming proper initial height and retract timing.
Problem signs demand immediate attention and adjustment. Voltage fluctuations exceeding 10% indicate potential issues with either the feedback system or power supply stability. Delayed height corrections suggest the need for PID tuning adjustments in the control software. Frequent THC disengagement during tests often points to incorrect sensitivity settings or faulty sensor connections. Each of these symptoms provides valuable diagnostic information for fine-tuning system performance.
Maintaining detailed test records transforms occasional verification into an ongoing quality assurance process. Documenting the date and machine hours at the time of testing creates a maintenance history that helps identify wear patterns. Recording the material type and thickness used for testing establishes performance baselines for different applications. Voltage parameters and any adjustments made during testing provide crucial reference points for future troubleshooting. This documentation becomes invaluable when diagnosing intermittent issues or planning preventative maintenance schedules.
Innovations in CNC Automation: PoStep25-256 and the Technologies That Make It Shine
Maximizing Efficiency in CNC Plasma Cutting: A Step-by-Step Guide to Setup and Control
Conclusion: The Path to Cutting Excellence
Achieving consistent, high-quality plasma cutting results demands attention to four interconnected elements. Proper torch height control establishes the foundation, maintaining the precise arc distance that defines cut quality. Careful plasma cutter setup ensures all machine parameters align with material requirements and project specifications. The THC screen set Mach3 provides the necessary interface for monitoring and adjusting these parameters during CNC operations. Finally, regular torch height control tests verify the entire system’s readiness, preventing costly errors before they occur.
Operators who implement this comprehensive approach reap measurable benefits. Consumable life extends significantly, often achieving 30-50% longer nozzle and electrode lifespan. Nozzle collision incidents approach zero as potential issues are identified and corrected during testing. Most importantly, cut quality remains consistent across jobs, reducing rework and improving overall productivity. Whether working in a hobbyist shop or production environment, these practices elevate plasma cutting from a simple metal severing process to a precision fabrication technique capable of producing professional-grade results consistently.
The time invested in proper setup and testing ultimately pays dividends through reduced material waste, fewer machine downtime incidents, and higher quality finished products. In metal fabrication, where precision directly translates to profitability, mastering these elements separates adequate results from exceptional ones. By treating the torch height control test not as an optional step but as an essential part of the cutting process, operators ensure their equipment performs at its full potential for every job.