Computer Numerical Control (CNC) machines have revolutionized manufacturing, enabling precision, efficiency, and automation. However, optimizing a CNC system requires integrating advanced hardware and software components seamlessly. In this article, we will explore four critical elements that can significantly enhance CNC performance:
PoKeys57CNC – A versatile motion controller that simplifies CNC operations.
Mach4 Tool Setter – An essential tool for automating tool length measurement.
Mach4 Laser – A powerful addition for engraving and alignment tasks.
CNC Wiring – The backbone of a reliable and efficient CNC setup.
Each of these components plays a vital role in ensuring smooth CNC operations. We will delve into their functionalities, benefits, and how they integrate into a cohesive system.
PoKeys57CNC – The Heart of Advanced CNC Control
The PoKeys57CNC is a versatile and powerful motion controller designed to streamline CNC machine operations. Whether you’re working with a DIY CNC router, a milling machine, or a laser engraver, integrating the PoKeys57CNC can significantly enhance precision, simplify wiring, and improve overall system responsiveness.
What Is the PoKeys57CNC?
The PoKeys57CNC is a USB-based motion controller that connects directly to Mach4, one of the most popular CNC control software platforms. Unlike traditional breakout boards, the PoKeys57CNC integrates multiple functions into a single compact device, reducing wiring complexity and improving signal integrity. It supports up to 6 axes of motion control, digital I/O, spindle control, and encoder feedback—making it an all-in-one solution for CNC enthusiasts and professionals alike.
Key Features and Benefits
Simplified Wiring – The PoKeys57CNC reduces the need for multiple breakout boards and complex wiring setups. Its integrated design minimizes signal interference and ensures reliable communication between the CNC software and machine components.
Plug-and-Play Compatibility with Mach4 – Unlike some motion controllers that require extensive configuration, the PoKeys57CNC works seamlessly with Mach4, allowing for quick setup and calibration.
Advanced Motion Control – With support for microstepping and adjustable acceleration/deceleration curves, the PoKeys57CNC ensures smooth and precise motor movements, reducing vibration and improving cut quality.
Expandable I/O Options – Additional digital and analog inputs/outputs can be added via expansion modules, making the PoKeys57CNC adaptable to various CNC setups.
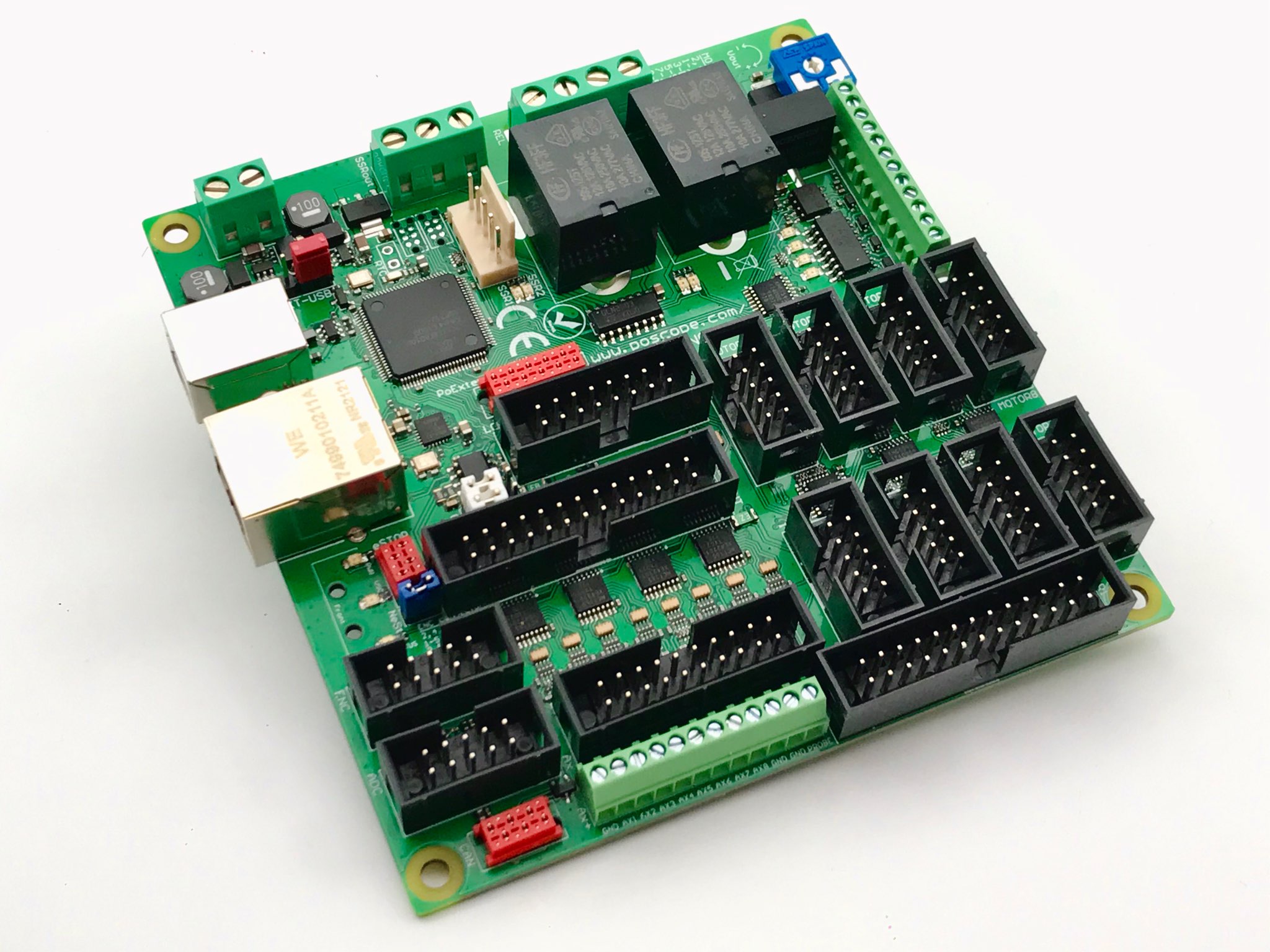
Practical Applications
The PoKeys57CNC is ideal for:
- CNC Routers – Ensuring high-speed, accurate cuts in wood, plastic, and aluminum.
- Milling Machines – Providing stable motion control for metalworking applications.
- Laser Cutters & Engravers – Enabling precise laser positioning and power modulation.
Why Choose PoKeys57CNC Over Traditional Controllers?
Many CNC users rely on generic breakout boards, but these often introduce latency and wiring complications. The PoKeys57CNC eliminates these issues by integrating critical functions into a single, high-performance unit. Its real-time processing capabilities ensure that Mach4 commands are executed without delay, resulting in smoother machine operation.
For anyone looking to upgrade their CNC system, the PoKeys57CNC offers a perfect balance of performance, simplicity, and expandability. In the next chapter, we’ll explore another crucial component: the Mach4 Tool Setter, which automates tool measurement for flawless machining.
Mach4 Tool Setter – Precision Automation for Flawless Tool Measurement
Achieving consistent accuracy in CNC machining depends heavily on precise tool measurement. Even a minor deviation in tool length can lead to ruined workpieces, wasted material, and costly downtime. This is where the Mach4 Tool Setter proves indispensable—a specialized device designed to automate and streamline the tool measurement process, ensuring repeatable precision with every operation.
Understanding the Mach4 Tool Setter
The Mach4 Tool Setter is an electronic probe that integrates seamlessly with Mach4 CNC software, allowing for automatic tool length measurement. Unlike manual methods that rely on operator skill and are prone to human error, the Mach4 Tool Setter provides a fast, reliable, and hands-off approach. When a tool is loaded, the machine gently lowers it onto the tool setter’s contact surface, which sends a signal to Mach4, instantly recording the exact tool length offset.
How the Mach4 Tool Setter Enhances CNC Workflow
One of the most significant advantages of the Mach4 Tool Setter is its ability to reduce setup time. Machinists no longer need to manually measure each tool with calipers or height gauges—instead, the CNC machine handles the process automatically. This is particularly beneficial in production environments where multiple tool changes occur frequently. The Mach4 Tool Setter also eliminates inconsistencies between operators, ensuring that every tool is measured with the same level of precision.
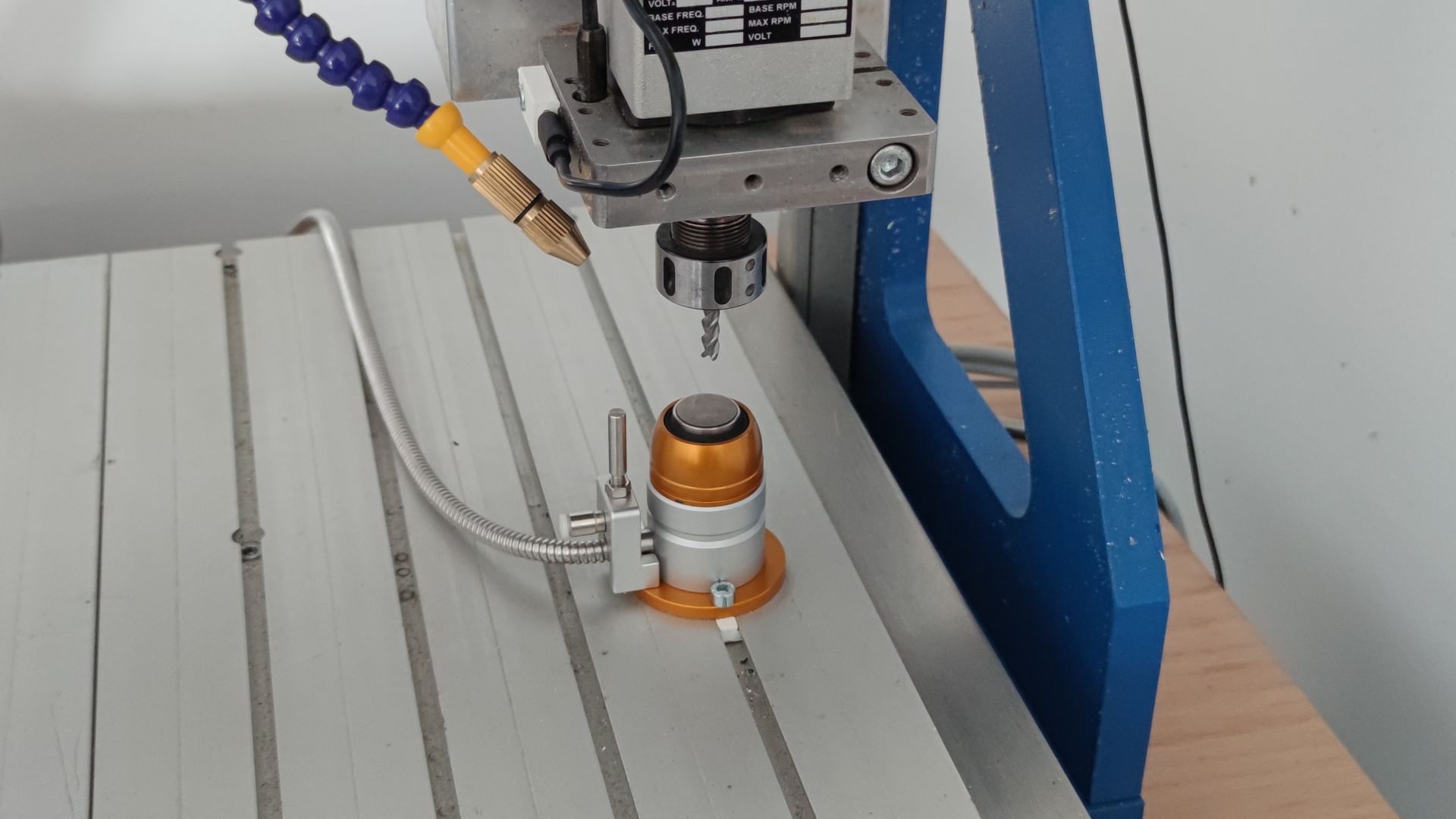
Beyond speed and accuracy, the Mach4 Tool Setter improves safety. Manual tool measurement requires the operator to be near the spindle, increasing the risk of accidents. With an automated tool setter, the machine performs the measurement cycle independently, minimizing human interaction with moving parts.
Integration with PoKeys57CNC and Mach4
When paired with a motion controller like the PoKeys57CNC, the Mach4 Tool Setter becomes even more powerful. The PoKeys57CNC’s fast signal processing ensures that tool measurement data is transmitted to Mach4 without delay, allowing for immediate adjustments before machining begins. This seamless integration means fewer errors, smoother operations, and higher overall efficiency.
Applications Across Different CNC Machines
The Mach4 Tool Setter is not limited to a single type of machine. Whether used on a CNC router, milling machine, or engraver, it delivers consistent results. For woodworking, where tool wear can affect cut quality, the Mach4 Tool Setter allows for quick re-measurement between jobs. In metalworking, where tolerances are tight, it ensures that each tool is perfectly calibrated before cutting begins.
Why Every CNC Operator Should Consider a Tool Setter
While some may view a tool setter as an optional accessory, its impact on productivity and precision makes it a worthwhile investment. The Mach4 Tool Setter transforms an error-prone manual task into a fully automated process, freeing up operators to focus on more critical aspects of machining.
In the next chapter, we’ll shift focus to another valuable addition to the CNC workflow—the Mach4 Laser, which opens up new possibilities for engraving, alignment, and precision marking.
Mach4 Laser – Expanding CNC Capabilities with Precision Light
The integration of laser technology with CNC systems has opened new frontiers in precision manufacturing. When combined with Mach4 control software, a Mach4 Laser system transforms standard CNC machines into versatile tools capable of engraving, cutting delicate materials, and performing ultra-fine alignment tasks with remarkable accuracy.
The Role of Mach4 Laser in Modern CNC Operations
A Mach4 Laser system typically consists of a laser module, power supply, and control interface that integrates directly with the Mach4 software environment. Unlike traditional spindle-based machining, laser systems apply concentrated thermal energy rather than mechanical force, allowing for intricate work on materials that would otherwise be difficult to machine conventionally. The Mach4 Laser interface provides precise control over laser power, pulse frequency, and movement speed – all critical parameters for achieving consistent results.
Key Advantages of Laser Integration
One of the most significant benefits of implementing a Mach4 Laser system is its ability to handle materials that challenge conventional cutting tools. Thin plastics, veneers, anodized aluminum, and even certain fabrics can be processed cleanly without the risk of material deformation from mechanical pressure. The non-contact nature of laser processing eliminates tool wear concerns, while the pinpoint accuracy enables reproduction of details as fine as 0.1mm.
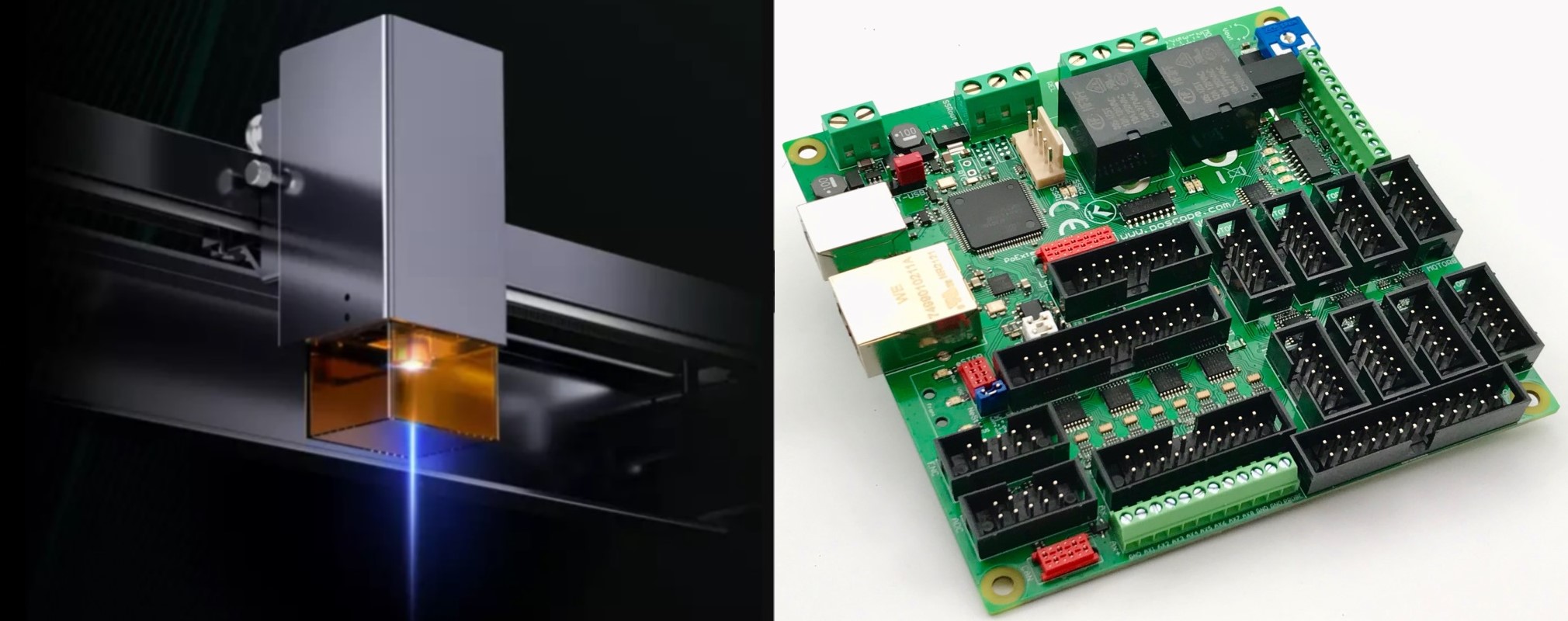
The Mach4 Laser system shines particularly in engraving applications. Whether marking serial numbers on metal parts or creating intricate decorative patterns, the laser maintains consistent depth and clarity across the entire workpiece. This capability proves invaluable for manufacturers requiring permanent part identification or artisans creating customized products.
Technical Considerations for Implementation
Successful Mach4 Laser integration requires attention to several technical factors. The laser wavelength must match the intended materials – CO2 lasers excel with organic materials, while fiber lasers work better with metals. Safety systems including enclosure interlocks, fume extraction, and emergency stops must be properly configured within Mach4’s I/O control. The software’s laser-specific plugins allow for precise control of power modulation during curved movements, preventing burn marks at direction changes.
Synergy with Other System Components
When combined with the PoKeys57CNC controller, a Mach4 Laser system achieves even greater performance. The controller’s high-speed processing ensures smooth laser movements and accurate power synchronization, particularly important when executing complex vector patterns. For operations requiring both laser work and conventional machining, the system can automatically switch between laser and spindle tools using the Mach4 Tool Setter for height calibration.
Practical Applications Across Industries
The versatility of Mach4 Laser systems finds applications in numerous fields. Electronics manufacturers use them for PCB etching and component marking. Sign makers employ them for cutting acrylic letters and engraving decorative elements. Even in heavy industries, lasers assist with precise alignment markings for assembly processes. The ability to store and recall specific laser parameters within Mach4 makes these systems ideal for job shops handling diverse projects.
As we’ve seen, adding laser capability through Mach4 significantly expands what’s possible with CNC technology. In our final technical chapter, we’ll examine the foundational element that ties all these advanced components together – proper CNC Wiring practices that ensure reliable, interference-free operation.
CNC Wiring – The Nervous System of Your Machine
Behind every high-performance CNC system lies an often overlooked yet critical component: CNC wiring. Just as the nervous system carries signals throughout the human body, proper CNC wiring forms the essential network that connects controllers, drives, sensors, and power supplies into a cohesive, reliable machine. Neglecting wiring quality can lead to erratic behavior, lost steps, or even catastrophic failures – making it one of the most important aspects of CNC system design.
The Fundamentals of Effective CNC Wiring
High-quality CNC wiring begins with understanding signal types and their requirements. Stepper and servo motor cables demand careful shielding to prevent electromagnetic interference from corrupting step and direction pulses. Analog signals from probes and sensors require twisted pair configurations to maintain signal integrity. Power distribution wiring must account for voltage drop over distance, especially in machines with large work envelopes. The PoKeys57CNC controller’s centralized design helps minimize wiring complexity, but proper implementation remains crucial regardless of controller choice.
Interference and Noise Mitigation
One of the most common issues in CNC wiring stems from electrical noise – unwanted signals induced into control wiring from nearby power cables or machinery. This manifests as unexplained machine movements, false limit switch triggers, or communication errors. Proper separation of power and signal cables, using shielded cables with proper grounding, and implementing ferrite cores on sensitive lines can dramatically improve reliability. The Mach4 Tool Setter and Mach4 Laser systems particularly benefit from clean wiring, as their precision measurements can be skewed by even minor electrical interference.
Wiring Organization and Maintenance
Beyond electrical considerations, physical CNC wiring layout significantly impacts long-term reliability. Cable carriers (drag chains) protect moving wires from fatigue, while proper strain relief at connection points prevents gradual wire breakdown. Labeling all connections saves hours of troubleshooting during maintenance or upgrades. Implementing modular connectors where possible – such as between machine sections or for removable components – simplifies future modifications. These practices prove especially valuable when integrating complex systems like the Mach4 Laser, where additional components demand careful cable routing.
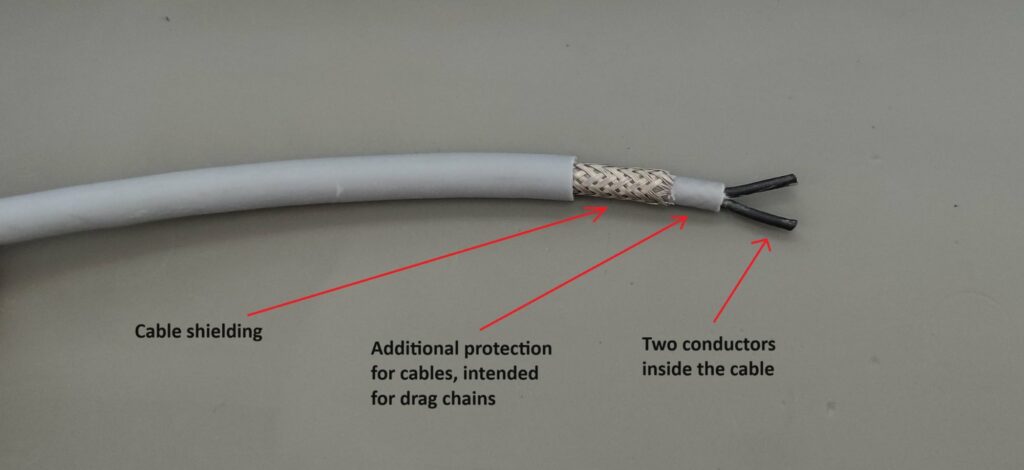
Safety Considerations in Wiring Design
Proper CNC wiring must address safety beyond basic functionality. Emergency stop circuits should use normally closed contacts wired in series, ensuring any break in the circuit stops the machine. Separate grounding paths for control electronics and chassis prevent ground loops. Overcurrent protection devices must be properly sized for each circuit branch. These measures become particularly critical when high-power components like spindles or lasers operate alongside sensitive control electronics like the PoKeys57CNC.
Future-Proofing Your Wiring Infrastructure
Thoughtful CNC wiring accommodates future expansions. Leaving spare conductors in cable runs, using larger-than-necessary wireways, and documenting all connections make adding features like a Mach4 Tool Setter or upgraded drives significantly easier. Implementing a structured wiring approach from the beginning saves countless hours compared to retrofitting changes to an existing tangled wiring harness.
As we’ve seen, CNC wiring forms the critical foundation supporting all other advanced components. Just as a symphony orchestra relies on each musician playing in perfect harmony, a CNC machine requires every wire to carry its signal cleanly and reliably. In our conclusion, we’ll examine how these four elements – PoKeys57CNC, Mach4 Tool Setter, Mach4 Laser, and proper CNC wiring – work together to create a complete, high-performance CNC system.
Maximizing CNC Efficiency with PoKeys57CNC and Mach4 Probing Solutions
Building a Cohesive, High-Performance CNC System
The journey through these four critical components—PoKeys57CNC, Mach4 Tool Setter, Mach4 Laser, and CNC wiring—reveals how each element contributes to creating a CNC system that is greater than the sum of its parts. When properly integrated, they form a seamless workflow that maximizes precision, efficiency, and reliability in any machining environment.
Synergy Between Components
At the core of this system lies the PoKeys57CNC, a motion controller that bridges hardware and software with remarkable efficiency. Its ability to handle multiple axes, digital I/O, and spindle control makes it the central nervous system of the CNC machine. When paired with the Mach4 Tool Setter, the system gains automated precision, eliminating manual measurement errors and reducing setup time. The Mach4 Laser expands the machine’s capabilities beyond traditional cutting, enabling engraving, marking, and fine-detail work that would be impossible with conventional tooling.
However, none of these components can perform at their best without proper CNC wiring. Like the vascular system of a living organism, wiring ensures that power and signals flow cleanly and reliably. Poor wiring introduces noise, interference, and potential failures, while a well-organized wiring harness ensures that the PoKeys57CNC, Mach4 Tool Setter, and Mach4 Laser all communicate flawlessly with the machine’s drives and sensors.
The Impact on Modern CNC Machining
Adopting these technologies transforms a basic CNC machine into a versatile, high-performance system. The PoKeys57CNC simplifies motion control while maintaining precision, the Mach4 Tool Setter automates tedious calibration tasks, and the Mach4 Laser unlocks new creative and industrial applications. Meanwhile, robust CNC wiring ensures that these components work together without hiccups, reducing downtime and maintenance headaches.
Innovations in CNC Automation: PoStep25-256 and the Technologies That Make It Shine
Maximizing Efficiency in CNC Plasma Cutting: A Step-by-Step Guide to Setup and Control
Final Thoughts
Whether you’re a hobbyist building a DIY CNC router or a professional optimizing a production workshop, integrating these four elements will elevate your machining capabilities. The PoKeys57CNC provides the control, the Mach4 Tool Setter ensures accuracy, the Mach4 Laser adds versatility, and proper CNC wiring ties it all together. By focusing on each of these aspects, you can build a CNC system that delivers consistent, high-quality results—every time.